eBook
Manager’s Guide to Simulating Aeroacoustics
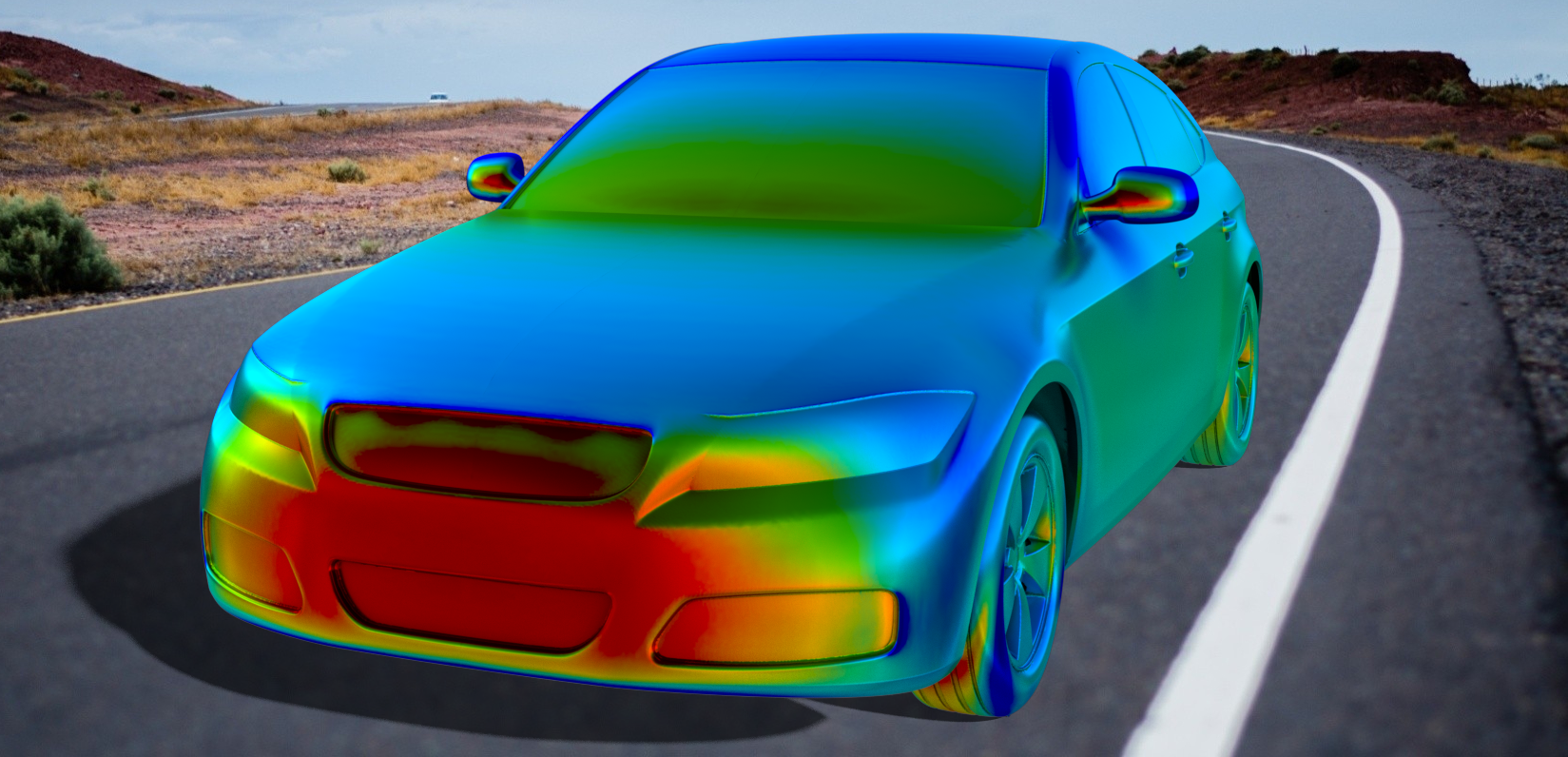
Overview
Introduction
In today’s fast-paced world of innovation and technological advances, sound—particularly unwanted or harmful noise—has become a paramount concern in various industries. Whether it’s the mighty roar of a jet engine or the rhythmic swoosh of a wind turbine, the soundscapes that modern technologies create have direct implications on user experience, environmental harmony, and regulatory compliance. This is where the science of aeroacoustics and its simulation comes into play.
But why should this matter to you as a manager? Beyond the technical intricacies that engineers grapple with, simulating aeroacoustics presents a host of strategic decisions and opportunities for businesses. It’s not merely about noise control; it’s about enhancing product value, meeting evolving regulatory standards, and carving a competitive edge in the market.
This guide aims to equip managers with an understanding of aeroacoustic simulations from a business and strategic perspective. We’ll explore its value proposition, cost implications, risk management, and the broader impact on business strategy. As we navigate through, you’ll discover how aeroacoustic simulations can be a pivotal tool in your managerial toolkit, enabling informed decisions that drive innovation and growth. Welcome aboard this enlightening journey into the world of aeroacoustics from a manager’s lens.
Understanding the Basics
Aeroacoustics is the study of noise generated by air movement, particularly in and around objects. At its core, it’s about comprehending how fluid flows—like air—produce sound, especially when they interact with various surfaces. But for businesses and managers, it’s much more than that. Let’s break it down.
A CLOSER LOOK AT AEROACOUSTICS
For managers, having a general overview of aeroacoustics is essential for making informed decisions. But if you’re curious about the technicalities or want to bridge the gap between management and engineering, getting a more in-depth grasp can be invaluable.
Our detailed Engineer’s Guide to Simulating Aeroacoustics delves into the nitty-gritty of aeroacoustic simulations, from understanding core principles to advanced simulation techniques. Whether you’re looking to converse more effectively with your technical teams or just expand your knowledge, this guide is the perfect starting point.
Explore the Engineer’s Guide to Simulating Aeroacoustics here.
Aeroacoustics: A Quick Overview
Aeroacoustics isn’t a new field. Ever since humans took to the skies or designed high-speed trains, the challenge has always been not just about making them move fast but doing so with minimal noise. The primary goal in aeroacoustics is to predict, measure, and control noise. Although there’s a world of math, physics, and computer modeling behind it, the real-world applications are what’s truly fascinating. From designing quieter aircraft engines (Figure 1) and wind turbines to optimizing airflow around buildings for urban noise reduction, aeroacoustics has a wide range of applications.
The Business Impact of Noise
Noise isn’t just an environmental or auditory concern; it’s a business concern. In various sectors, noise can influence customer satisfaction, product usability, and even sales. For instance, a quieter airplane cabin can be a major selling point for commercial airliners, as it directly enhances the flight experience. Similarly, aircraft manufacturers are under constant regulatory pressure to reduce noise footprints around airports, which affects routes, schedules, and profitability.
Furthermore, in a world that is more and more conscious about sustainability and quality of life, noise pollution is gaining more attention from the public and regulatory bodies. Consumers and regulators are pushing companies to limit their acoustic footprints. This has direct implications for branding, public relations, and market positioning. Not to mention, failure to comply with noise regulations can lead to hefty penalties and legal consequences.
Expertise in aeroacoustics isn’t just a technical need; it’s a strategic imperative. Businesses well-versed in the field will be prepared to navigate the challenges and opportunities that sound—and the lack of it—present in today’s market landscape.
Strategic Importance of Aeroacoustic Simulations
Aeroacoustic simulations occupy a distinct niche in the vast world of simulations and modeling. Although the technical side is left to engineers and experts, from a strategic vantage point, these simulations offer unique advantages that can shape the trajectory of businesses. Let’s explore how.
Enhancing Product Design and Efficiency
In today’s consumer-driven market, the quest for perfection in product design is relentless. Aeroacoustic simulations offer insights that can profoundly influence the design phase. Consider the automotive industry; a car’s acoustic profile, from the wind noise at high speeds to the cabin’s insulation from external sounds, can be a deciding factor for potential buyers. By simulating the aeroacoustics, manufacturers can refine designs, ensuring a harmonious balance between aesthetics, functionality, and acoustic comfort.
Meeting Regulatory Requirements
Noise emission regulations grow more stringent by the day, especially in aviation and renewable energy. For example, the European Union Aviation Safety Agency recently introduced the Environmental Protection Technical Specifications, the first noise certification standard for electric vertical take-off and landing (eVTOL) aircraft (Figure 2). Failing to meet such standards can lead to substantial fines, operational restrictions, or even product recalls. Aeroacoustic simulations empower businesses to anticipate and address potential regulatory hurdles even before a product hits the market. This proactive approach safeguards against potential penalties and streamlines the certification process, speeding up time-to-market.
Gaining a Competitive Edge
In an increasingly crowded marketplace, differentiation is key. Aeroacoustic simulations can be that edge. A quieter airplane, a less noisy wind turbine, or a silent-running car can stand out, appealing to a consumer base that values tranquility. Moreover, showcasing a commitment to reducing noise pollution can considerably enhance a brand’s reputation, signaling a commitment to environmental responsibility and customer well-being.
Beyond these direct benefits, there’s a key advantage to leveraging aeroacoustic simulations: future readiness. As urban areas become denser and the global push toward sustainability intensifies, noise management will be more critical than ever. Businesses that harness the power of aeroacoustic simulations today will be better positioned to lead tomorrow. In sum, aeroacoustic simulations aren’t just about decibels and airflow. They’re strategic tools, shaping product trajectories, informing business decisions, and creating pathways to market leadership.
Main Challenges Facing Managers
Aeroacoustic projects present a distinct set of challenges for managers. These challenges go beyond the regular hurdles faced in typical projects, and they demand a nuanced understanding, effective communication, and adaptable strategies. Here, we list the primary challenges faced by managers when simulating aeroacoustics and provide insights into navigating them effectively.
Although the challenges for managers in aeroacoustic simulations are multifaceted, they are not insurmountable. With the right strategies, tools, and mindset, managers can navigate these challenges and turn them into opportunities for growth, innovation, and success.
Overcoming Managerial Challenges
Having outlined the challenges of simulating aeroacoustics, let’s shift our focus to a potential solution available for today’s managers. We’ll explore a contemporary tool with technological advancements that are paving the way for more cost-effective, efficient, and accurate simulations.
Introducing Fidelity CharLES
Fidelity CharLES isn’t just any computational fluid dynamics (CFD) solver—it’s software crafted to bring high-resolution simulations to the fingertips of design engineers, promising speed and accessibility like never before. Whether you’re working with graphics or central processing units, CharLES is optimized to function seamlessly. It offers a versatile approach to simulating various applications, including jet engine combustors and vehicle external aerodynamics.
Picture a tool that is fine-tuned for the flow conditions often found in aeroacoustic simulations, with algorithms designed to handle complicated scenarios with ease and precision. CharLES is able to tackle aeroacoustic problems with high accuracy and stability using advanced numerical methods. It’s all about honing in on the sound, and CharLES does this brilliantly.
Furthermore, the solver boasts a user-friendly design that is sophisticated yet practical and is suitable for seasoned experts and newcomers alike. Imagine having a tool with an intuitive interface that promises a smooth workflow (Figure 3) from setup to execution. This is a useful feature for users venturing into the world of CFD without a deep background in the field. And for those looking to add a personal touch, CharLES offers a high level of customizability to meet your specific needs.
Why CharLES?
Now, you might be wondering what makes CharLES stand out in the crowded landscape of CFD software. Well, it’s all about its ability to accurately, efficiently, and cost-effectively predict and address complex CFD challenges, such as aeroacoustic noise, turbulent mixing, flow separation, transition, turbulent shear stress and heat transfer, as well as combustion and emissions.
Predictive
The uniqueness of CharLES’s solver lies in its utilization of large-eddy simulations (LES), which offers a level of precision and reliability that’s rare in many commercial CFD tools. Its LES model is grounded in the fundamental principles of physics, ensuring stability and accuracy. The outcome? A model that captures complex flow phenomena with an accuracy that is simply unparalleled, as demonstrated in Figure 4.
Fast
In today’s dynamic design landscape, the speed at which you obtain solutions is paramount. Regardless of their accuracy, simulations that take a long time to complete risk lagging behind the evolving design curve. CharLES’s solvers are designed for extensive parallel processing and scalability and are proficient at maximizing vast computational resources to deliver timely and meaningful results. Paired with advanced pre- and post-processing utilities, its system ensures rapid and insightful outcomes.
CharLES has the means to distribute the computational load across a spectrum of processors or computing nodes, bringing efficiency to setups ranging from small clusters to supercomputers. It’s not just about distribution—it’s about intelligent allocation through advanced load-balancing algorithms, ensuring every processor is a powerhouse of productivity, minimizing idle time, and amplifying computational efficiency.
CharLES goes a step further, optimizing memory usage to negate the need for excessive memory allocation, which is essential in large-scale simulations where memory can be a bottleneck. Its architecture is a testament to versatility, providing scalability across a myriad of platforms and operating systems. CharLES adapts and is ready to meet your computational demands head-on, whether you’re working on a local workstation, a high-performance computing cluster, or navigating cloud-based infrastructures. The solver also offers a window into computational performance through real-time monitoring features, empowering users to dynamically fine-tune their modeling process to optimize efficiency in long-running simulations.
Cost-Efficient
CharLES’s solvers have historically been optimized for conventional CPU-based clusters. However, as technology progressed, the focus shifted towards accelerated node architectures, which currently dominate the top-tier supercomputing platforms. In these systems, the majority of computational capacity and memory bandwidth is vested in GPUs. CharLES’s solvers are skilled at harnessing various accelerated-node designs, leading to enhanced simulation efficiency and potential reductions in expenses and energy consumption. The solver excels by harnessing GPU architectures, slashing computational time when pitted against traditional CPU setups. Figure 5 demonstrates this advantage, where there is 9x throughput for the same cost of CPU and 9x lower cost and 17x less energy for the same CPU throughput. This is a game-changer for large-scale simulations demanding swift turnaround times.
…9x throughput for the same cost of CPU and 9x lower cost and 17x less energy for the same CPU throughput.
Cost-Benefit Analysis
Any strategic decision, especially one that revolves around adopting new technologies or methodologies like aeroacoustic simulations, should be grounded in a clear awareness of the costs involved and the potential returns. Let’s dissect the cost-benefit dynamic of integrating aeroacoustic simulations into your business strategy.
The Upfront Costs
Implementing aeroacoustic simulations does come with its set of costs. High-fidelity simulations require robust computational infrastructure, including powerful servers and specialized software tools. Additionally, having the right human resources—experts knowledgeable in aeroacoustics—is essential. This might involve hiring new talent or training existing employees. Specialized software for aeroacoustic simulations may also come with hefty licensing fees, especially for industry-leading tools.
The Hidden Savings
Although the initial costs might seem substantial, the savings accrued over time can offset these. With accurate simulations, the need for multiple physical prototypes can decrease, leading to significant savings in materials, labor, and time. Moreover, proactively addressing noise concerns can prevent costly regulatory fines and potential litigations. Last but not least, testing at full scale in an anechoic chamber is cumbersome and expensive. Changes to designs can be tested and validated virtually, eliminating the costs of physical redesigns.
The Long-Term Benefits
Beyond immediate savings, aeroacoustic simulations can yield benefits that, while hard to quantify, can notably influence a business’s bottom line. Being recognized as an industry leader in noise management can boost brand reputation, potentially influencing customer purchasing decisions. Also, products compliant with global noise standards can access a broader range of markets without regulatory hassles. Finally, insights from simulations can lead to novel product features or entirely new product lines, opening avenues for revenue generation.
Weighing the Scales
At the end of the day, the decision to integrate aeroacoustic simulations boils down to a simple question: Does the strategic advantage and long-term benefits outweigh the initial investments? For many businesses, especially those in sectors where noise management is paramount, the answer leans heavily toward a resounding “yes.”
Realizing this cost-benefit interplay helps managers make informed decisions, aligning technical investments with key business goals and ensuring sustainable growth in an ever-evolving market landscape.
CharLES in Action
Aeroacoustic simulations have broad industrial relevance, encompassing everything from supersonic aircraft noises to fan sounds. Table 1 summarizes some notable endeavors where CharLES has proven its worthiness, including VTOL rotor and sedan noise predictions with Honda R&D as well as NASA’s fan noise source diagnostic test (SDT).
|
SDT (low noise OGV) |
Full-Scale Sedan |
Multibladed Rotors |
Grid Resolution (million control volumes) |
142 |
118 |
30 (multibladed rotor); 137 (full-scale eVTOL aircraft) |
GPU Run-Time |
≈6 hours on 40 Nvidia V100 PCIe GPUs |
≈1.5 hours on 32 Nvidia V100 GPUs |
<12 hours on 40 AMD Mi210 GPUs (full-scale eVTOL aircraft)
|
CPU Run-Time |
≈24 hours on 4096 AMD 7H12 Rome CPUs |
≈6 hours on 2560 AMD EPYC CPUs |
36 hours on 2016 SGI ICE XA Intel Xeon E5 2697 v4 CPUs (full-scale eVTOL aircraft) |
Relative Error (Overall Sound Pressure Level) |
1.12% |
Within ± 5 dB of experimental values |
<2% for all multibladed rotors |
Investigation of VTOL Rotor Noise with Honda R&D
Multi-bladed VTOL rotors—commonly used in modern drones and urban transportation vehicles—were studied to determine the precision and cost-effectiveness of high-frequency aeroacoustic simulations. Researchers evaluated a range of rotor configurations, from two up to five blades, and then compared the findings with data from Honda’s wind tunnel tests. There was a noticeable uptick in noise as the number of rotor blades increased—a trend that matched the experimental data. Furthermore, CharLES was used to simulate a full-scale eVTOL aircraft, complete with eight VTOL rotors and a pair of propellers, underscoring the software’s widespread potential and efficiency, especially when leveraged with GPU acceleration.
Noise Predictions for a Full-Scale Car with Honda R&D
Honda R&D analyzed the sound profile of a sedan cruising at 120 kph. The goal was to compare its predictions with real-world wind tunnel tests. The simulations were performed using two different grid resolutions, and the refined version helped pinpoint interesting airflow patterns, especially around the A-pillar. Such patterns can influence the car’s performance and the noise it produces. To ensure the accuracy of the simulations, the outcomes were compared to actual wind tunnel data. The simulation results closely agreed with the real-world data. It was also found that using specialized graphics hardware (GPUs) made the simulations run considerably faster than using traditional computer processors (CPUs).
NASA’s Fan Noise Source Diagnostic Test
In a joint effort with NASA, CharLES was used to perform a fan noise SDT. The primary goal was to identify how different outlet guide vane (OGV) designs affected the fan’s aerodynamics and noise levels. The comprehensive computational setup included the entire test section, nacelle, as well as the full annulus of the fan and OGVs, which was simulated at 61.7% of its normal speed. Subsequently, the low noise OGV design was found to reduce the noise level by about 2 dB—a significant difference—and the simulations matched the experiments. Notably, CharLES demonstrated impressive accuracy even with a relatively coarse mesh.
CharLES consistently achieves a high degree of accuracy compared to real-world experiments. By harnessing the power of GPU acceleration, the solver offers fast simulations without compromising on detail. This software is available through conventional client site setups and dedicated cloud solutions, providing flexibility for diverse needs.
The Journey Ahead
Simulating aeroacoustic phenomena requires more than just technical prowess; it demands strategic oversight, robust collaboration, and astute decision-making. This guide is aimed at equipping managers with a holistic view of aeroacoustics that emphasizes the pivotal role they play in bridging technical details with overarching business goals.
As we explored the essentials, from learning the basics to risk management, a recurrent theme emerged: the imperative of teamwork. It’s not just about managers understanding the technicalities or engineers grasping the project goals. It’s about forging a unified alliance where both realms are in sync, driving projects toward unprecedented success.
Aeroacoustic simulations, with their profound implications for industries ranging from aerospace to automotive, are poised to shape the future. And in this future, managers equipped with the insights, tools, and strategies discussed in this guide will undoubtedly lead the charge.
As you step forth, armed with this knowledge, remember that in the world of aeroacoustics, it’s not just about sound and air. It’s about vision, foresight, and the relentless pursuit of excellence. Here’s to a future where your projects not only succeed but set benchmarks for innovation and quality.
Want to Learn More?
Your journey toward more efficient, innovative, and successful aeroacoustics simulations starts here. Connect with us by filling out the contact form below and unlock the full potential of your projects with the advanced solutions offered by Cadence.